The type of power supply chosen for LEDs is a decisive factor in ensuring reliable, long-lasting installations.To understand the issues involved in LED power supply, a distinction must be made between the power supply for LED components and LED lights.
Power Supply for LEDs
LED lighting diodes are powered by current since their luminous flux is in proportion to the current flowing through them.
Several diodes connected in series – which thus have the same current flowing through them – will each emit the same luminous flux. If diodes are connected in parallel, each LED receives the same voltage but a different current flows through them due to the dispersion effect on the current-voltage characteristic (I–V curve). As a result, each diode emits a different luminous flux.
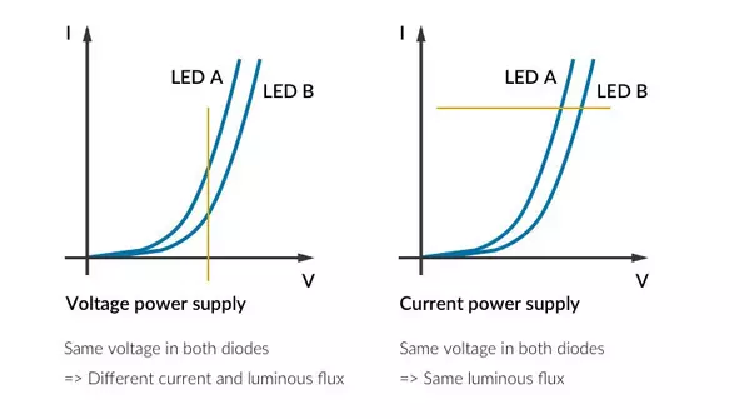
For each diode (LED) to work, approximately 3 Volts are required at its terminals. For example, a 5-diode series requires approximately 15 Volts at its terminals. To supply regulated current at an adequate voltage, Growling uses an electronic module called a driver.
There are 2 solutions:
1. External driver (fitted outside lights), with a Safety Extra-Low Voltage (SELV) (class III) power supply.
2. Internal driver (fitted inside lights), i.e. a subunit with an electronic module supplying regulated current.
This driver can be power supplied in 230V (class I or class II) or with a Safety Extra-Low Voltage (classe III), for instance in 24V.
Growling recommends the second power-supply solution since it gives 5 main benefits:
Voltage Power Supply for LED Lights – 5 Key Benefits
1. Safety Extra-Low Voltage is possible whatever the number of LEDs
LEDs should be installed in series to guarantee the same level of current in each one of them from one single source. As a result, the more LEDs there are, the higher the voltage in LEDs’ terminals. If it is an external driver, then the Safety Extra-Low Voltage is quicly over. Integrating a driver inside lights enables an entire installation to be powered by Safety Extra-Low Voltage (SELV), regardless of how many light sources there are.
2. More reliable installation
Installation engineers have expertise in the wiring standard for LED lights connected in parallel, meaning that the final installation is simpler and more reliable.
3. Longer lasting lights
Drivers provide extra protection, especially against rises in temperature and overvoltage, thus guaranteeing longer product life span.
4. Safer commissioning
Integrating LEDs’ power supply into a driver avoids mishandling in the field and improves their ability to withstand hot plugging. If you physically connect a luminaire with LEDs only to an external driver that is already turned on, then this may cause overvoltage in LEDs when you connect them, and therefore their destruction.
5. Easier maintenance
Any technical problems are seen more easily in LED lights with a voltage power supply (connected in parallel). Within the electronics world to which the LED belongs, the encountered faults are mostly due to open circuits (component or grilled tracks). With LEDs connected in parallel, only the relevant device shows up as faulty, whereas every device appears faulty in a series.
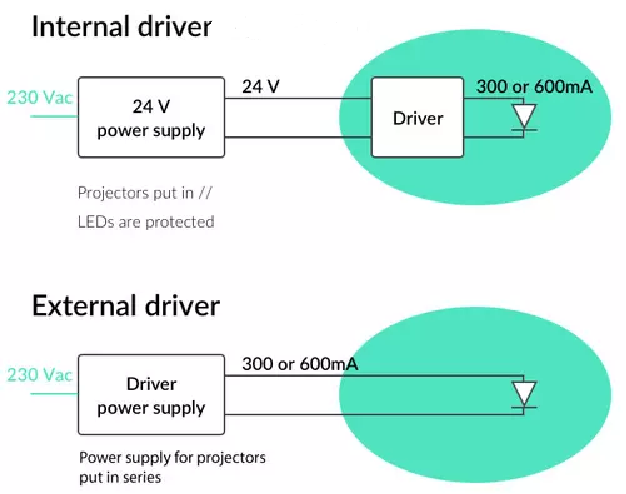
Voltage Power Supply for LEDs – What Does it Really Cost?
Contrary to conventional wisdom, LED lights with an integrated voltage power supply are not necessarily more expensive. In practice, the total installation cost is often higher for lights without an integrated driver. This is because installation engineers have to provide for a bigger number of external power supplies and adapt to installation constraints, especially for wiring. All this implies hidden costs.
Over the past years, Growling has been providing the best responses for our customers’ needs, finding the highest quality and most appropriate solution for each project. To this end, we integrate a 230 V power supply into lights whenever possible and also reduce general installation costs rather than product prices. For this reason, our teams always recommend lights with an internal driver powered by a voltage source (230 V or SELV).